Resources
Our latest thoughts on labeling and artwork management
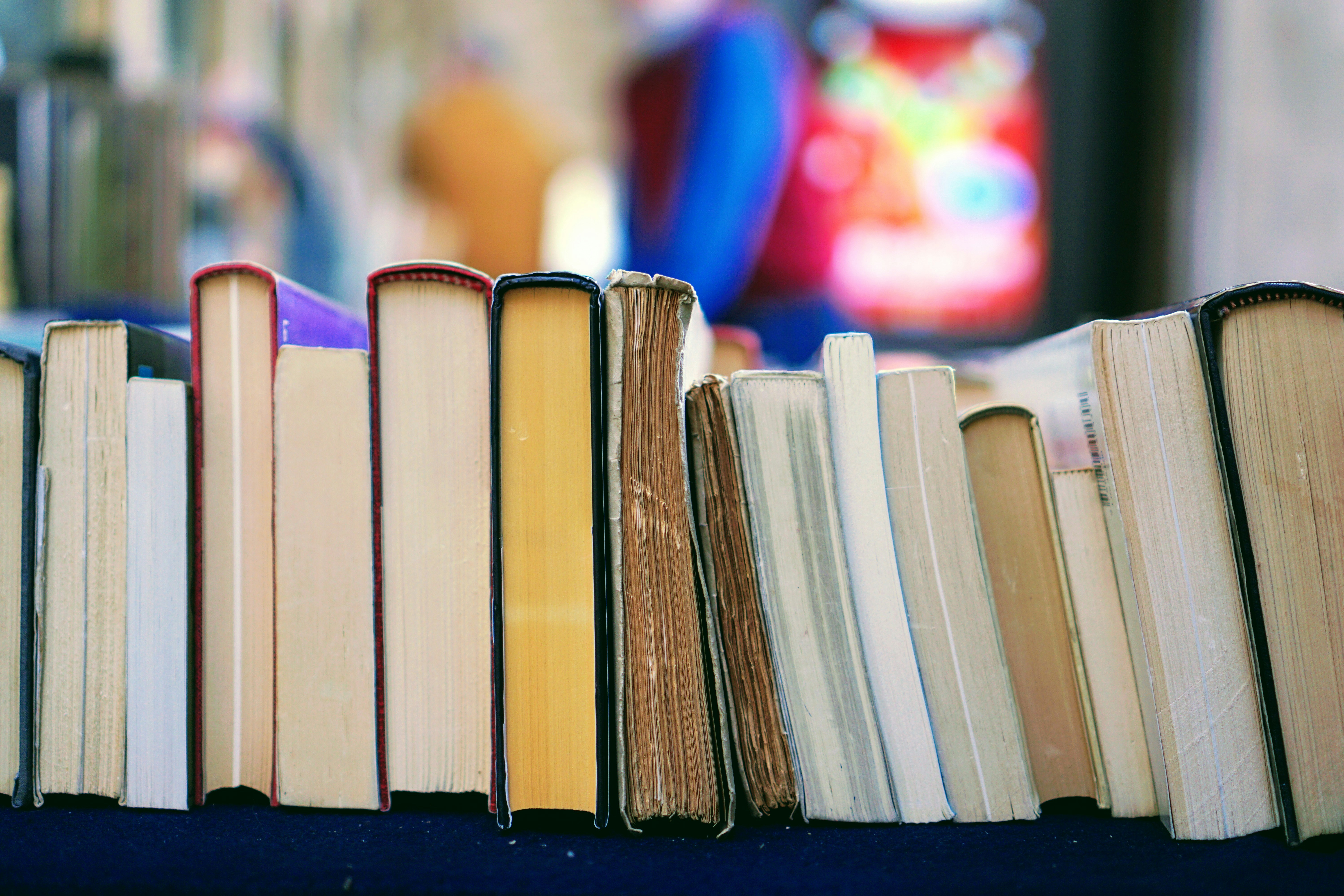
See featured resources
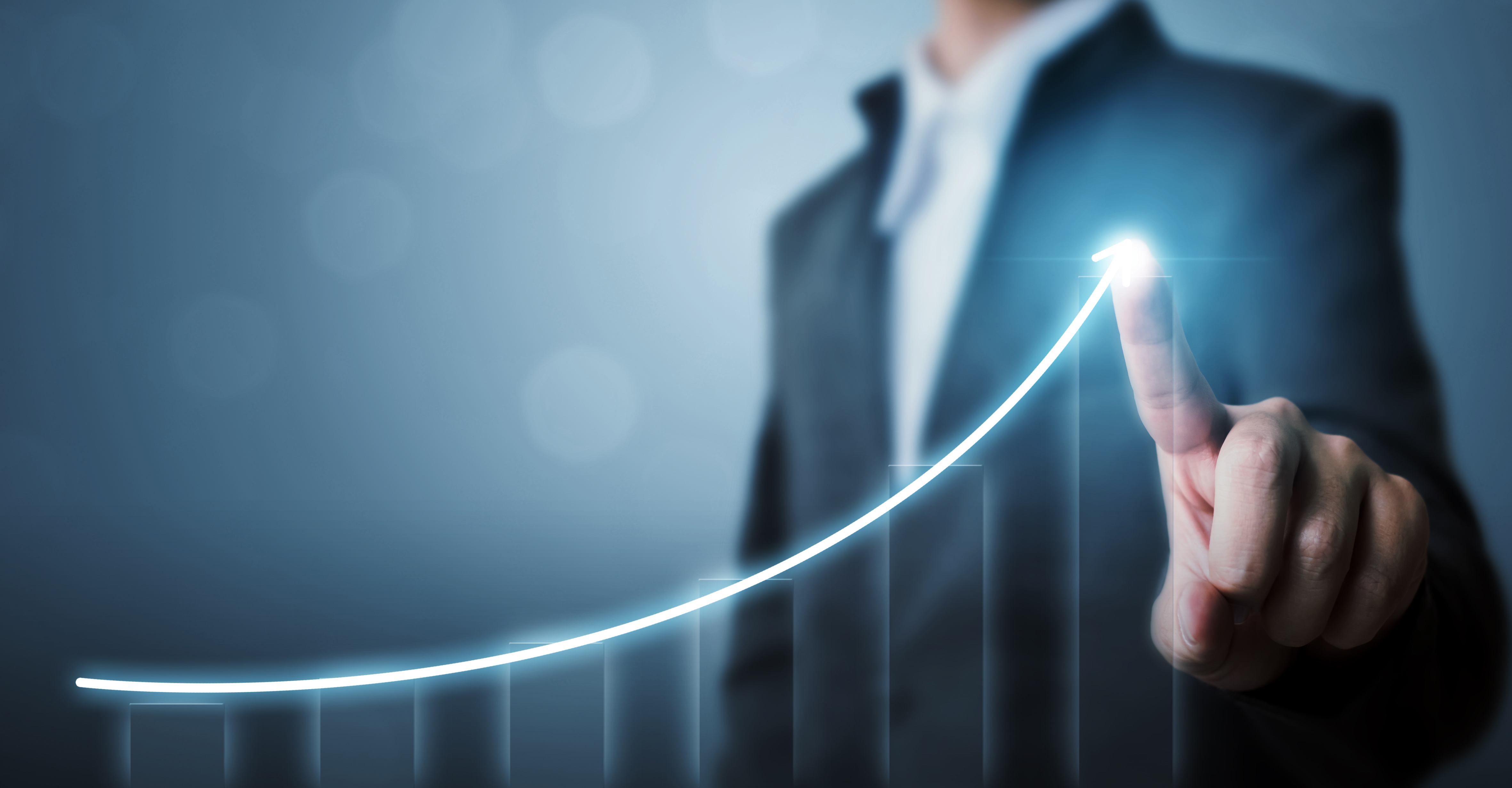
Other
Labeling Maturity Assessment
Are outdated labeling processes holding you back? Complete this 10 question survey to get your personalized assessment,...
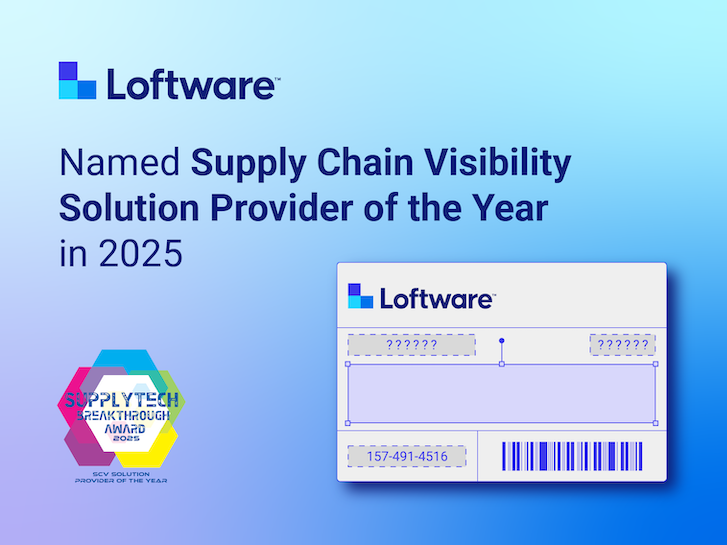
Press Release
Loftware Named Supply Chain Visibility Solution Provider of the Year in 2025 SupplyTech Breakthrough Awards
Loftware, a global leader in product identification and supply chain transparency, today announced that it has been...
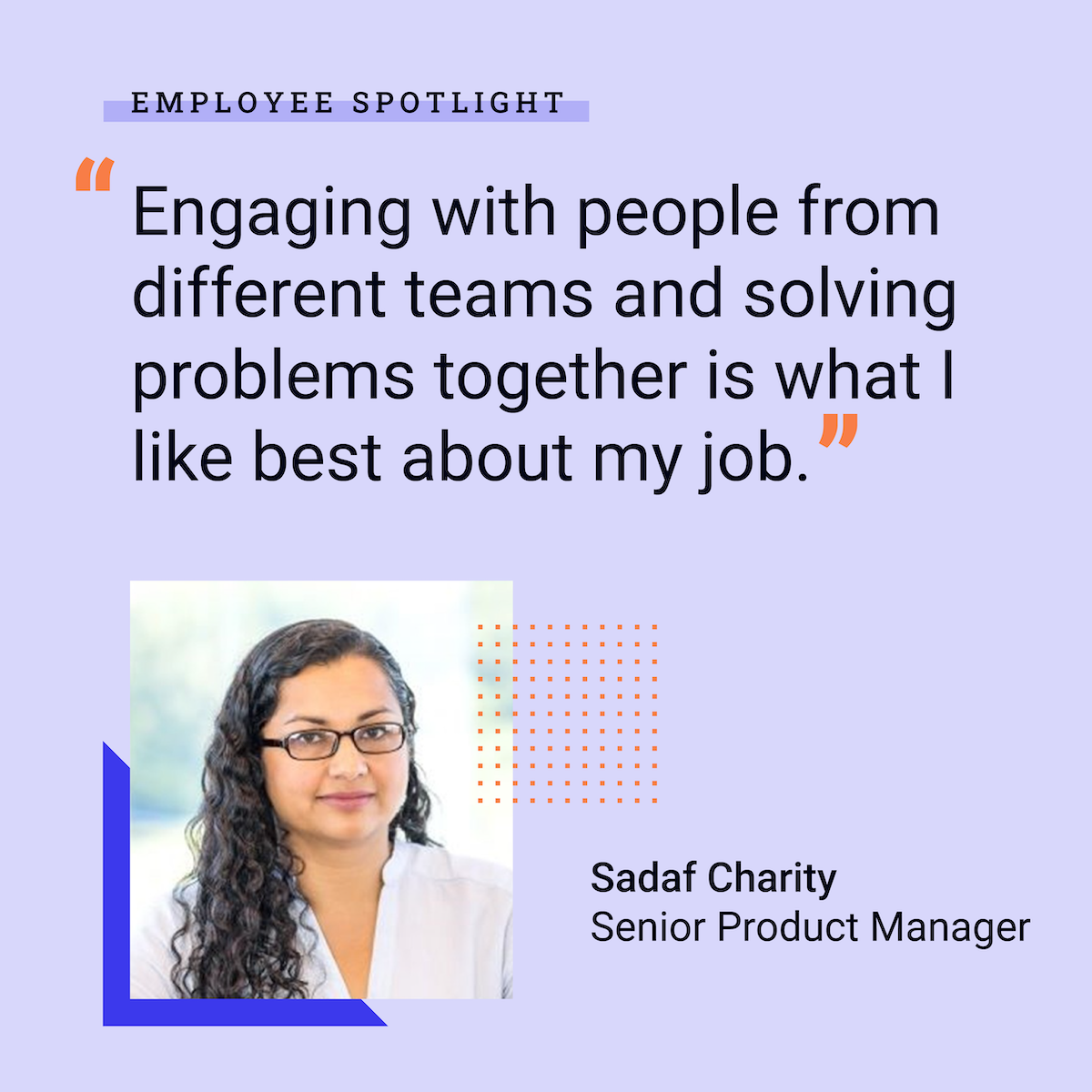
Blog
Employee Spotlight: Getting to know Sadaf Charity, Senior Product Manager
For this edition of our Employee Spotlight series, we’re excited to feature Sadaf Charity, a Senior Product Manager who...
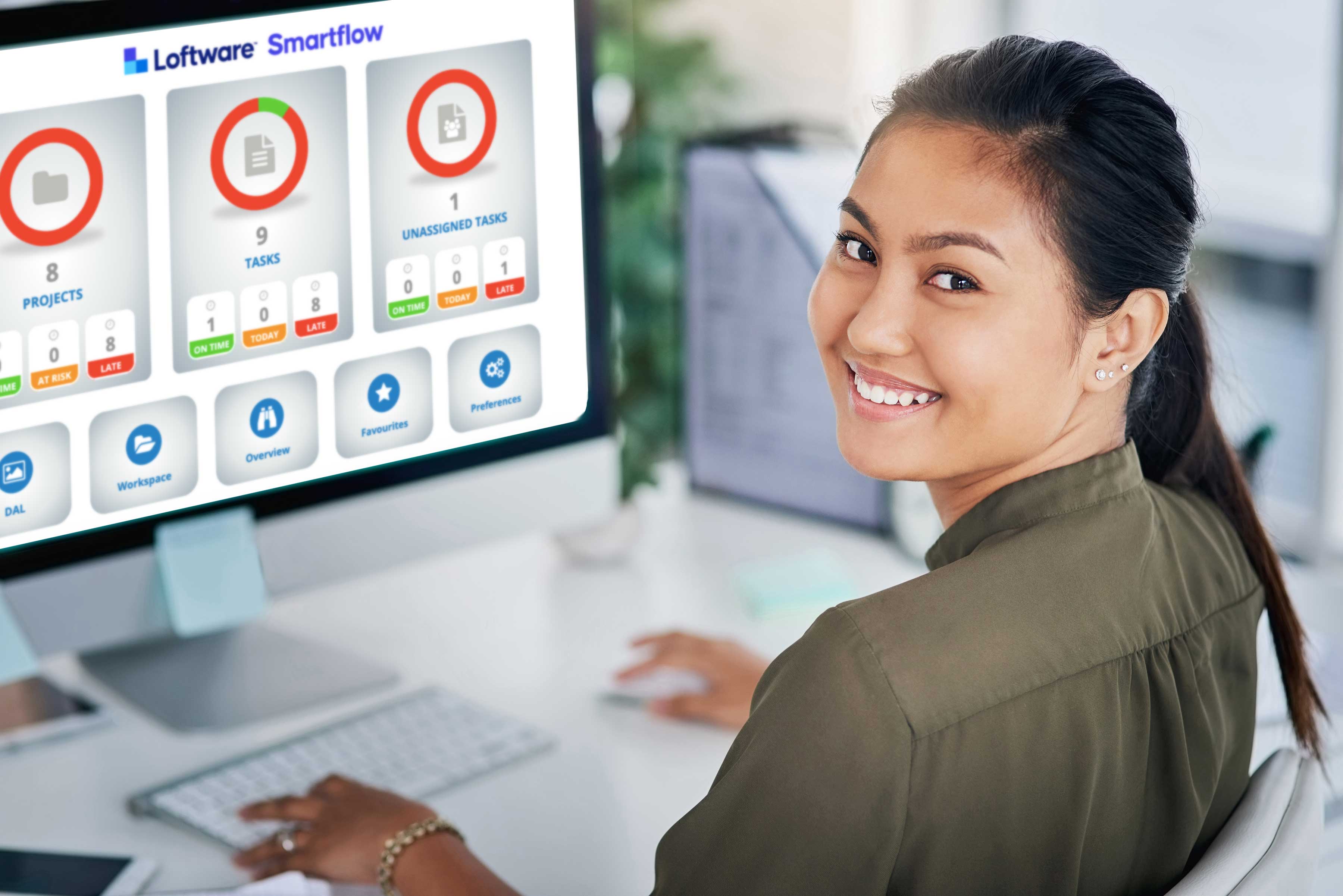
Webinar
Loftware Smartflow 27.2 Release Overview
Discover what's new in Smartflow 27.2! This release brings a number of updates that are especially valuable for...