Resources
Our latest thoughts on labeling and artwork management
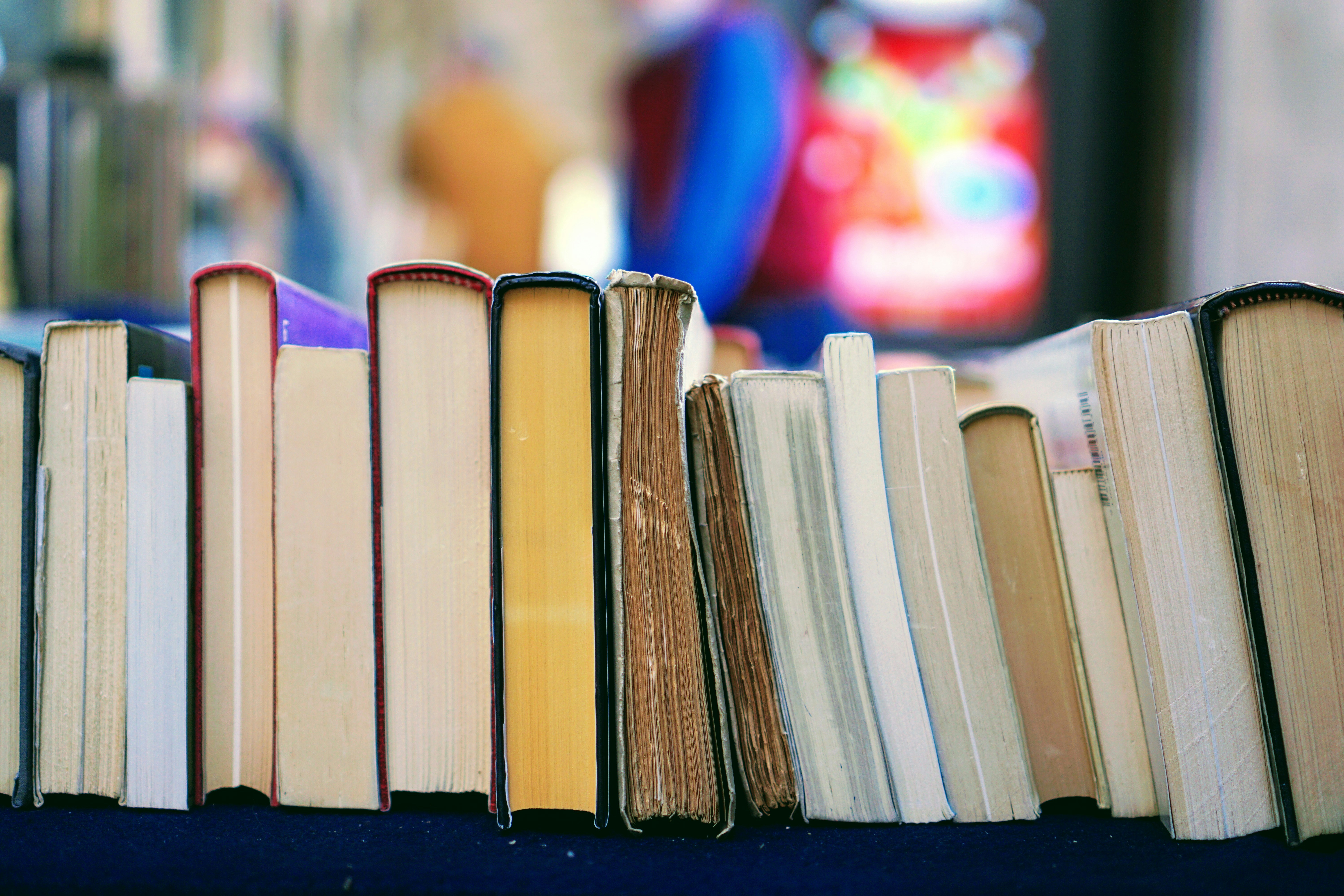
See featured resources
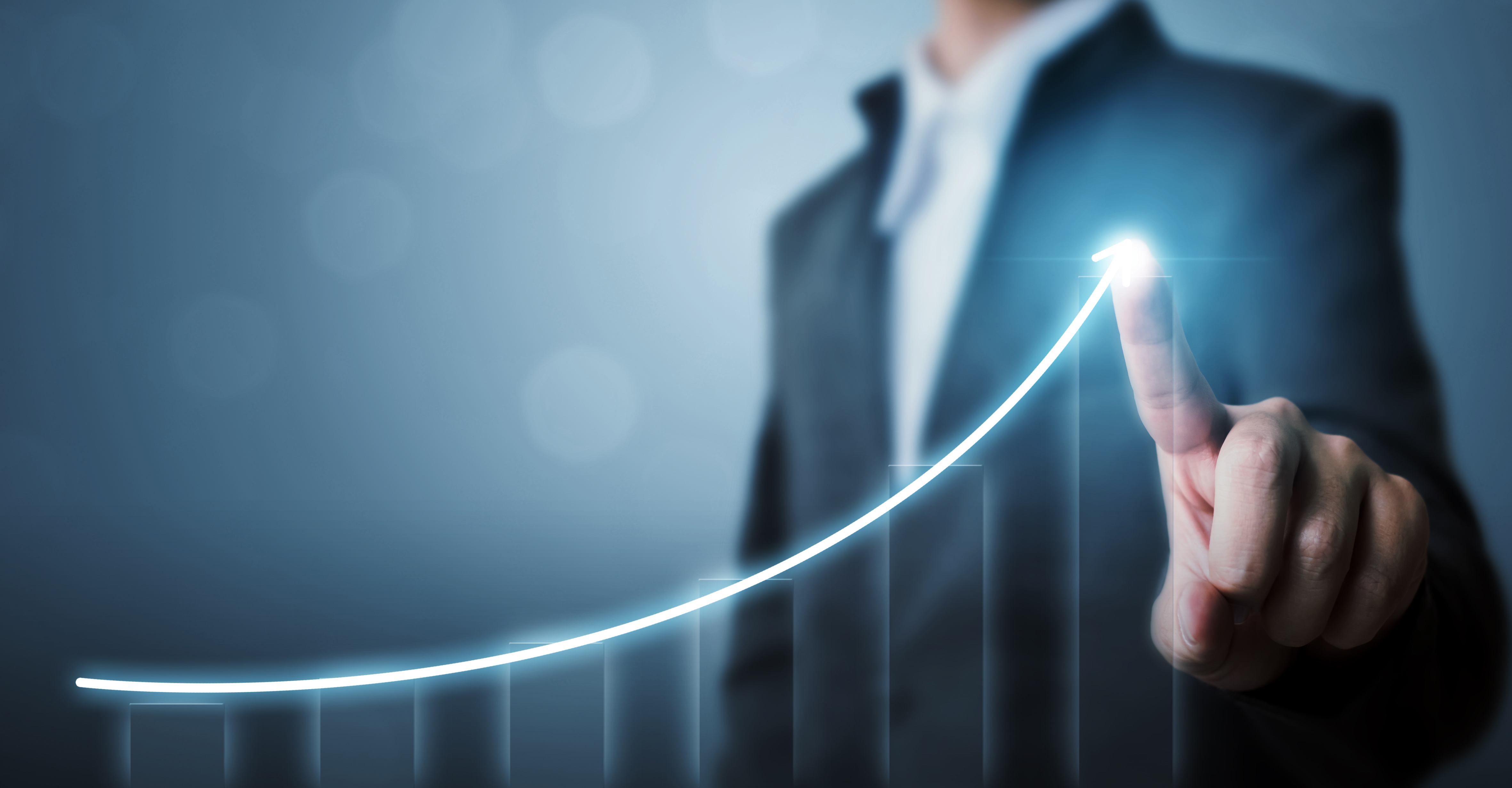
Other
Labeling Maturity Assessment
Are outdated labeling processes holding you back? Complete this 10 question survey to get your personalized assessment,...
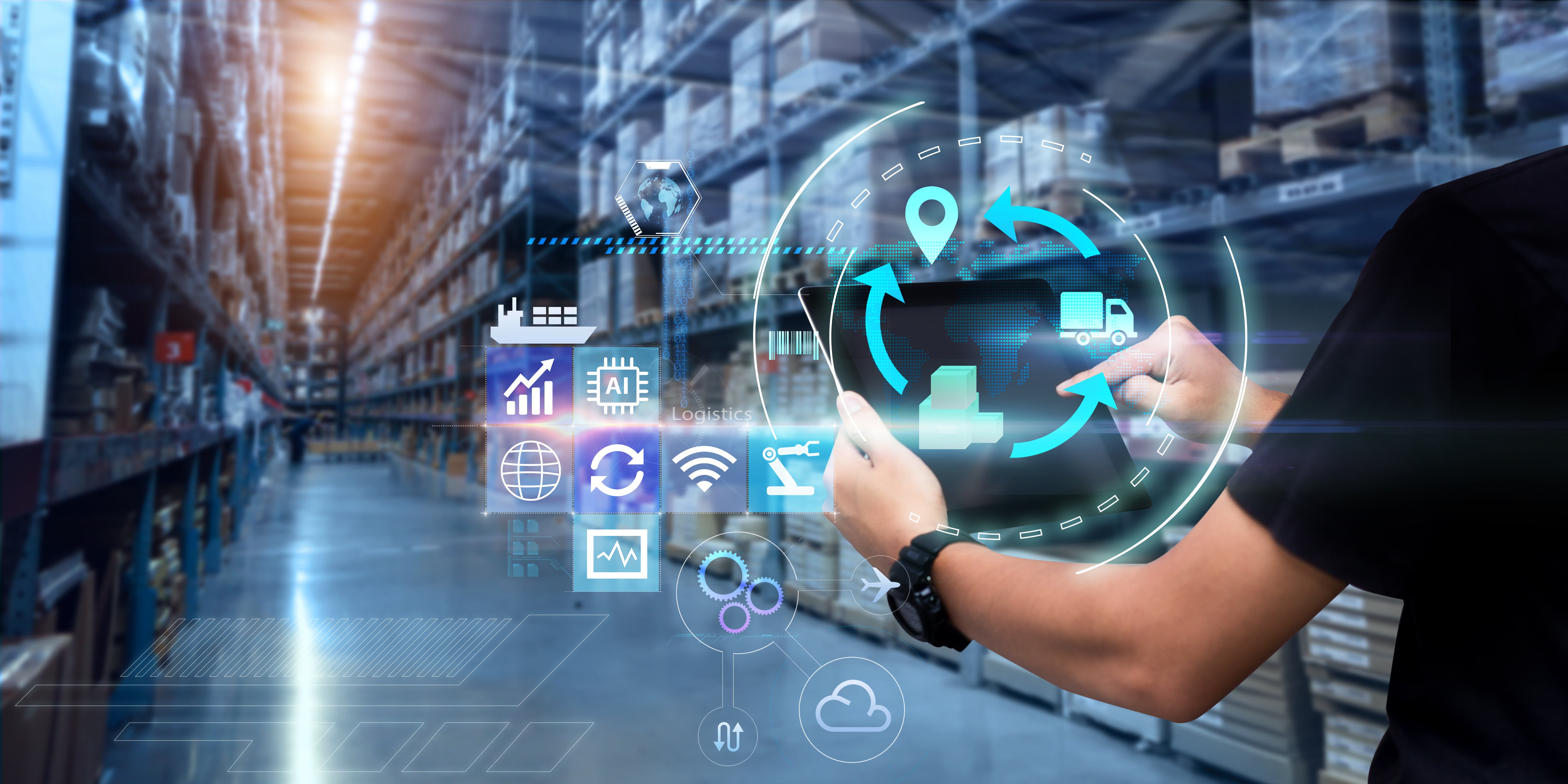
Blog
Building a resilient supply chain with data, traceability, and authenticity
The future of supply chain management is built on authenticity, compliance, and traceability. As industries evolve,...
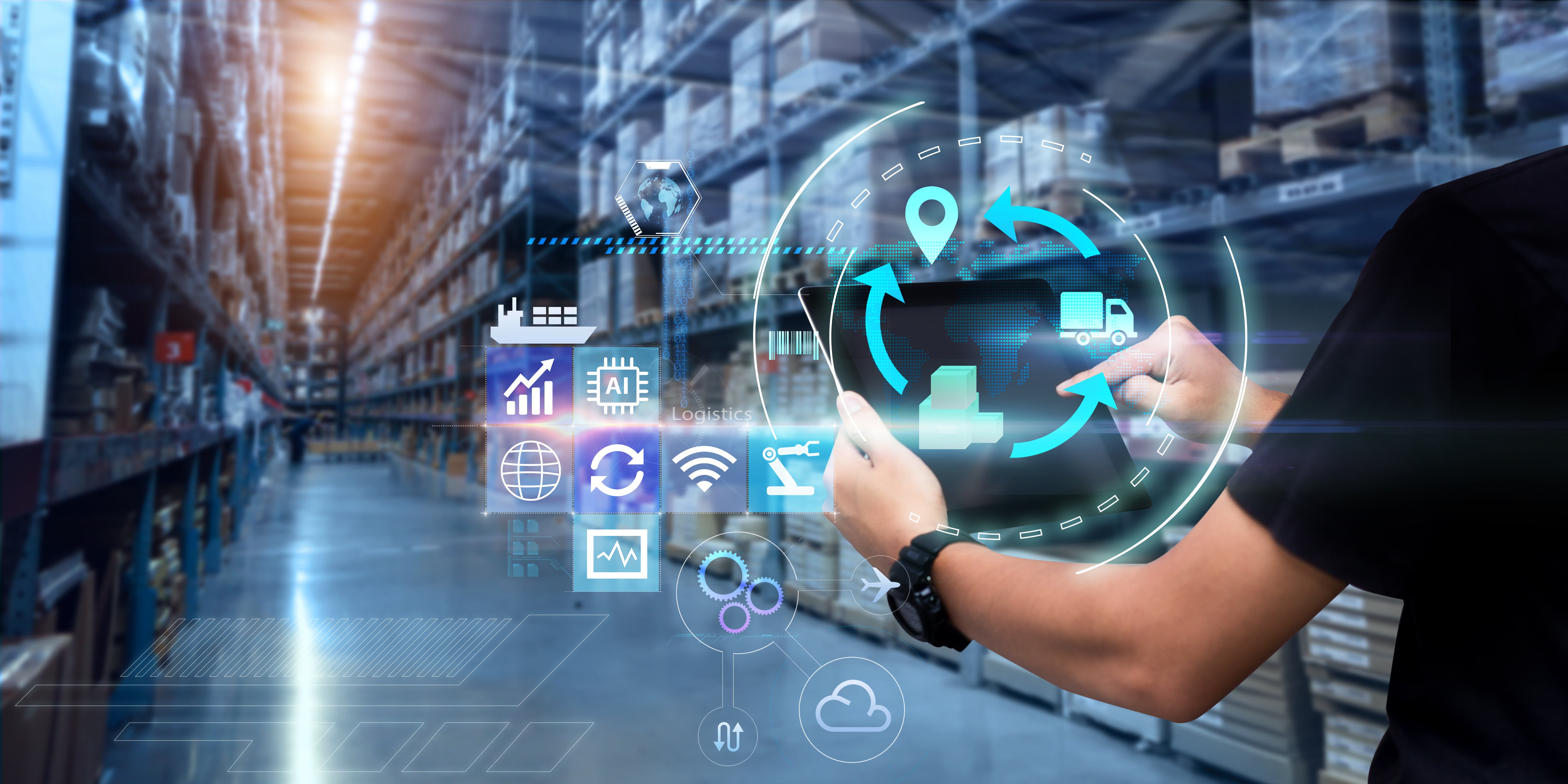
White Paper
VDC Research Paper: supply chain resilience through authenticity, compliance, and traceability
Explore key insights from VDC Research on how leading organizations are boosting agility, compliance, and...
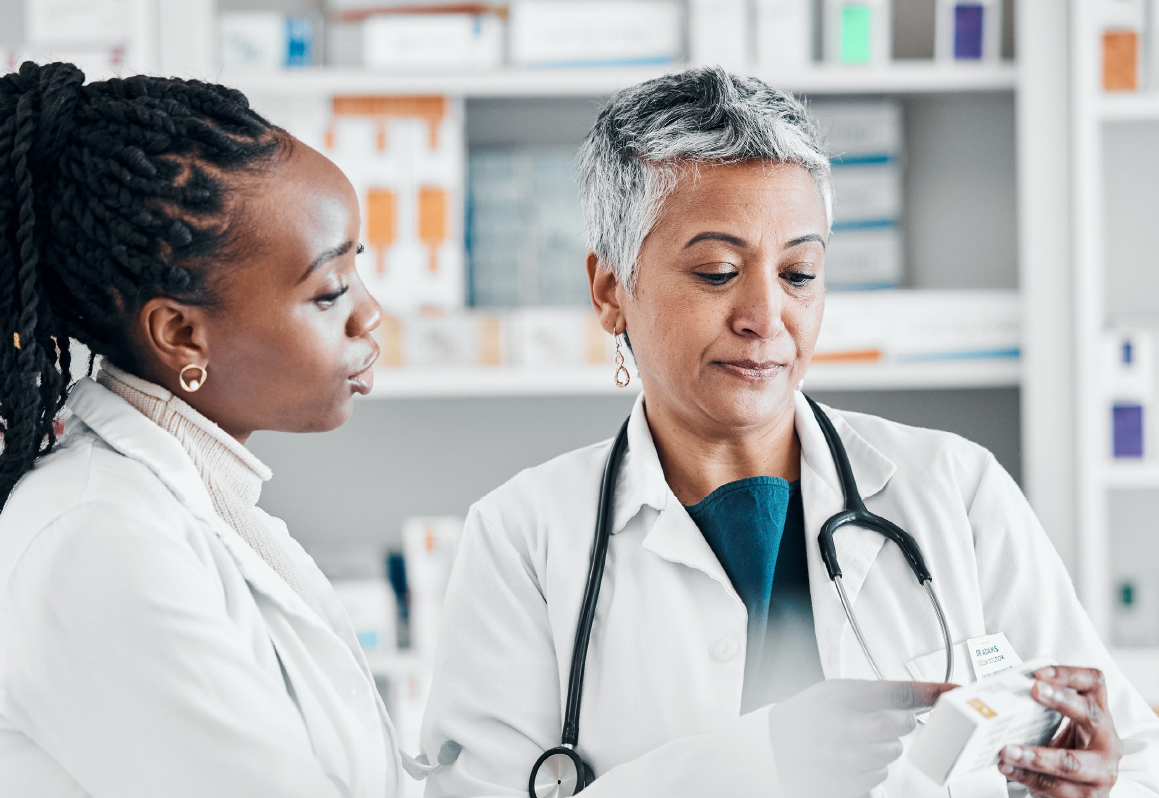
E-book
Q&A: Five imperative questions on challenges, innovation, and trends in pharma labeling
Get expert insights on labeling challenges and trends from industry leaders like Pfizer, LEO Pharma, and more. Download...